In the ever-evolving landscape of electronic devices and components, maintaining optimal performance and reliability is paramount. Electronic component cleaning plays a crucial role in ensuring the longevity and efficiency of these components. Traditional cleaning methods often fall short in addressing the challenges posed by the intricate structures of modern electronics. However, the emergence of advanced technologies, such as plasma technology, has opened up new possibilities for achieving precise and effective cleaning. “How To Use Plasma Technology For Electronic Component Cleaning”
Among the cutting-edge solutions, plasma technology has gained prominence for its ability to provide a thorough and efficient cleaning process. Unlike conventional methods, plasma cleaning involves the use of ionized gases to remove contaminants from surfaces at a microscopic level. This method offers several advantages, including precision, speed, and a reduced environmental impact.
Introduction to Plasma Cleaning
Plasma cleaning is a highly effective technique used in the cleaning and preparation of surfaces, particularly in the realm of electronic components. Unlike traditional cleaning methods, plasma cleaning operates in a gaseous state of matter known as plasma. Plasma laser cutter is created by introducing energy to a gas, causing it to ionize and form a mixture of charged particles, free radicals, and electrons. This unique state allows for a range of chemical reactions and interactions that make plasma cleaning a powerful and versatile tool in various industries.
Principles Behind Plasma Cleaning
The efficacy of plasma cleaning lies in its ability to generate a reactive environment that facilitates the removal of contaminants from surfaces. The reactive species present in the cnc plasma controller, such as ions and radicals, actively participate in chemical reactions with the contaminants, breaking them down into volatile byproducts. This process, known as chemical sputtering, effectively cleans the surface without the need for abrasive materials or harsh chemicals. Moreover, plasma cleaning can modify surface properties by introducing functional groups, making it a valuable technique in surface treatment and modification.
Types of Plasmasin Electronic Component Cleaning
Several types of plasmas are employed in electronic component cleaning, each tailored to specific requirements.
Oxygen Plasma: Oxygen plasmas are commonly used for organic contamination removal. The reactive oxygen species generated during the plasma process effectively break down and eliminate organic residues, leaving the surface pristine.
Argon Plasma: Argon plasmas are employed for inorganic contamination removal. The ions and radicals generated in an argon plasma are highly effective in removing metal oxides and other inorganic materials without adversely affecting sensitive electronic components.
Hydrogen Plasma: Hydrogen plasmas are utilized for reducing oxides and promoting surface passivation. This type of plasma is particularly beneficial for cleaning surfaces where oxygen-sensitive materials are present.
Nitrogen Plasma: Nitrogen plasmas find applications in removing hydrocarbons and other organic contaminants. The reactive nitrogen species assist in breaking down and removing complex organic molecules from surfaces.
Advantages of Plasma Cleaning

Plasma arc cutting cleaning offers a significant advantage in terms of precision compared to traditional cleaning methods. The process involves the use of ionized gases that can reach even the smallest and most intricate surfaces, ensuring a thorough and effective cleaning. This level of precision is particularly beneficial in industries such as electronics and medical device manufacturing, where cleanliness at the microscopic level is crucial for optimal performance.
Enhanced Efficiency
Plasma cleaning stands out for its efficiency, as it eliminates the need for chemical solvents or abrasive materials often used in traditional cleaning processes. The ionized gases in plasma cleaning break down and remove contaminants without leaving any residue, resulting in a quicker and more efficient cleaning process. This not only saves time but also reduces the consumption of cleaning agents, contributing to cost-effectiveness.
Eco-Friendliness
One of the notable advantages of spark plasma sinterin cleaning is its eco-friendly nature. Traditional cleaning methods often involve the use of harsh chemicals that can be harmful to both the environment and human health. In contrast, plasma cleaning requires only a small amount of gas, typically air or other environmentally friendly gases. This makes it a more sustainable and eco-conscious choice, aligning with the increasing global focus on green technologies and practices.
Versatility Across Materials
Cleanair plasma exhibits a high level of versatility, making it suitable for a wide range of materials and surfaces. Whether dealing with delicate electronic components, medical instruments, or industrial machinery, plasma technology can adapt to various materials without causing damage. This versatility makes it an ideal choice for diverse applications and industries, providing a one-size-fits-all solution for cleaning needs.
Extended Equipment Lifespan
By ensuring a thorough and residue-free cleaning process, plasma technology contributes to extending the lifespan of equipment and components. Contaminants and residues can lead to corrosion and deterioration over time, impacting the performance and longevity of machinery. Plasma cleaning helps prevent such issues, thereby reducing maintenance costs and increasing the overall reliability of equipment.
Electronic Components Suitable for Plasma Cleaning
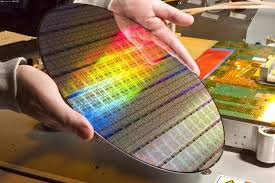
Plasma cleaning system is a highly effective technique used in various industries to remove contaminants from surfaces through ionized gases. This process requires specific electronic components to generate and control the plasma. In this context, selecting suitable electronic components is crucial for the efficiency and reliability of plasma cleaning systems.
Power Supplies
One of the key electronic components in a plasma cleaning system is the power supply. High-frequency power supplies are commonly employed to generate the required electrical energy for plasma generation. These power supplies must provide stable and controllable output to ensure a consistent plasma discharge.
RF Generators
Radio-frequency (RF) generators play a pivotal role in plasma system cleaning, providing the necessary RF power to create the plasma. These generators should be designed to operate at the desired frequency range and deliver precise power levels for optimal cleaning performance.
Gas Flow Controllers
Controlling the flow of gases is essential in plasma cleaning systems. Electronic gas flow controllers regulate the introduction of process gases into the plasma chamber. These components need to be capable of accurate and rapid adjustments to maintain the desired gas composition during the cleaning process.
Temperature and Pressure Sensors
Monitoring and controlling the temperature and pressure within the plasma arc chamber are critical for stable plasma conditions. Electronic temperature and pressure sensors ensure that the system operates within the specified parameters, preventing overheating or pressure fluctuations that could compromise the cleaning effectiveness.
Control Systems and Interfaces
The overall operation of a plasma cleaning system relies on sophisticated control systems and interfaces. Microcontrollers or programmable logic controllers (PLCs) are often employed to manage the various electronic components, ensuring coordinated and synchronized operation for efficient plasma tech cleaning.
Plasma Cleaning Equipment

RF plasma cleaning, crucial in industries like electronics, relies on specialized equipment for low-pressure plasma discharge. This process efficiently removes contaminants, ensuring pristine surfaces for subsequent applications such as coating and bonding.
Overview of Plasma Cleaning Equipment
Plasma cleaning is a highly effective method for removing organic and inorganic contaminants from surfaces through the use of low-pressure plasma drilling. The equipment required for plasma cleaning typically consists of a vacuum chamber, a power supply, and gas delivery systems. The vacuum chamber provides the controlled environment necessary for the generation of plasma, while the power supply delivers the energy needed to ionize the gas and create the plasma. Gas delivery systems ensure the introduction of the appropriate cleaning gas into the chamber.
Types of Plasma Cleaning Systems
Low-Pressure Plasma Cleaners
These systems operate at low pressures, typically in the range of 10 to 100 Pa, and are commonly used for delicate materials such as semiconductors and optics. Low-pressure plasma cleaners are suitable for removing thin organic films and contaminants without damaging the substrate.
Radiofrequency (RF) Plasma Cleaners
RF plasma cleaning systems use radiofrequency energy to generate plasma. These systems offer precise control over the cleaning process and are effective for a wide range of applications, including surface activation and modification. RF plasma cleaners are versatile and find applications in research, development, and industrial settings.
Microwave Plasma Cleaners
Operating at higher frequencies, microwave surface treatment plasma cleaners provide efficient and uniform plasma generation. These systems are often chosen for their ability to clean complex geometries and for their scalability in industrial applications. Microwave plasma cleaning is effective for removing both organic and inorganic contaminants.
Remote Plasma Cleaners
Remote energy plasma cleaners involve the generation of plasma at a distance from the substrate to be cleaned. This method allows for a gentler cleaning process, making it suitable for sensitive materials and electronics. Remote plasma cleaning is often preferred for applications where direct contact with the plasma may be undesirable.
Considerations for Choosing Plasma Cleaning Equipment
When selecting plasma cleaning equipment, factors such as the type of contaminants, substrate material, and desired cleaning outcome must be considered. Understanding the specific requirements of the application is crucial to choosing the most suitable plasma cleaning system for optimal results. As technology advances, new innovations in plasma cleaning equipment continue to emerge, offering enhanced precision, efficiency, and versatility in surface cleaning processes.
Also, Red More: What Age Can You Start Riding A Quarter Horse?
Case Studies
In the dynamic landscape of electronic component manufacturing, maintaining optimal cleanliness is paramount to ensure product quality and reliability. This case study explores the successful implementation of laser and plasma cutting technology for electronic component cleaning, showcasing its efficacy in overcoming specific challenges faced by industry leaders.
Resolving Residue Woes in Semiconductor Fabrication
- Challenge: A leading semiconductor manufacturer grappled with stubborn residues on delicate components, hampering production efficiency and compromising product performance.
- Plasma Cleaning Solution: Leveraging advanced plasma technology, the company implemented a tailored cleaning process that effectively eliminated residues without causing damage to the sensitive components. The plasma’s reactive ions and radicals efficiently broke down contaminants, resulting in enhanced yields and improved overall product quality.
Precision Cleaning for Aerospace Electronics
- Challenge: An aerospace electronics manufacturer faced stringent cleanliness requirements for components used in critical avionics systems. Traditional cleaning methods fell short in achieving the required precision and cleanliness standards.
- Plasma Cleaning Solution: By adopting plasma cleaning technology, the aerospace company achieved unparalleled precision in the removal of microscopic contaminants. The low-temperature, dry-cleaning process allowed for residue-free components, meeting the exacting standards of the aerospace industry and ensuring the reliability of electronic systems in challenging environments.
Tackling Flux Residues in PCB Assembly
- Challenge: A printed circuit board (PCB) assembly facility encountered challenges associated with flux residues, hindering the soldering process and affecting the overall functionality of electronic devices.
- Plasma Cleaning Solution: Introducing plasma technology into the PCB assembly line proved transformative. The plasma treatment efficiently removed flux residues from intricate board structures, ensuring optimal soldering conditions and improving the reliability of electronic devices. The dry and residue-free nature of the plasma cleaning process led to increased production throughput and a reduction in post-assembly inspections.
Future Trends in Plasma Cleaning Technology

In the ever-evolving landscape of industrial and research applications, plasma cleaning technology continues to play a pivotal role in ensuring the cleanliness and performance of various surfaces. As we look ahead, several key trends are poised to shape the future of macrofine plasma cleaning technology.
Miniaturization and Advanced Materials
Metal plasma technology is expected to witness a significant trend towards miniaturization to meet the demands of smaller and more intricate electronic components. As electronic devices continue to shrink in size, the traditional cleaning methods may become less effective. Innovations in plasma cleaning are likely to focus on adapting to these miniaturized structures. Moreover, advancements in materials science may lead to the development of plasma cleaning techniques specifically tailored for cleaning delicate and advanced materials used in electronic components.
Selective Surface Treatment
Future trends in plasma cleaning technology are anticipated to emphasize selective surface treatment. This involves the ability to precisely target and clean specific areas on electronic components without affecting the surrounding materials. Selective surface treatment is crucial for maintaining the integrity and functionality of complex devices. Enhanced control over plasma parameters and the development of intelligent march plasma systems may enable a more tailored and selective cleaning process.
Green Plasma Cleaning Solutions
An increasing focus on sustainability is likely to drive the development of eco-friendly or “green” plasma cleaning solutions. This trend involves reducing the environmental impact of cleaning processes by using environmentally friendly gases and optimizing energy consumption. Researchers and engineers are expected to explore novel plasma sources and gas mixtures that minimize waste and emissions while maintaining high cleaning efficiency.
Integration of Industry 4.0 Technologies
The integration of Industry 4.0 technologies into plasma cleaning systems is poised to transform the landscape of electronic component manufacturing. Smart sensors, data analytics, and real-time monitoring capabilities will enable more precise control and optimization of the pilot arc plasma cleaning process. This connectivity can lead to predictive maintenance, reduced downtime, and improved overall efficiency in electronic production facilities.
Plasma Cleaning for Flexible Electronics
As the demand for flexible electronics continues to rise, plasma arc light cleaning technology is anticipated to evolve to meet the unique challenges associated with these flexible substrates. Innovations may include the development of flexible plasma sources and techniques that can effectively clean and prepare the surfaces of bendable electronic components without compromising their structural integrity.
Conclusion
The adoption of plasma tech inc for electronic component cleaning aligns with the industry’s pursuit of precision, sustainability, and cost-effectiveness. As technology continues to evolve, plasma cleaning is poised to play a crucial role in shaping the future of electronic manufacturing, offering a cleaner, greener, and more efficient alternative to traditional cleaning methods. As researchers and engineers continue to refine and innovate in this field, we can anticipate further advancements that will solidify plasma technology’s place as a cornerstone in electronic component cleaning methodologies.
Frequently asked questions
Q: What is Plasma Technology in the context of electronic component cleaning?
Ans: Plasma technology utilizes ionized gases to generate a high-energy, reactive environment. In electronic component cleaning, it is employed to remove contaminants and ensure optimal performance.
Q: How does Plasma Technology clean electronic components?
Ans: Plasma cleaning works by creating a plasma discharge that bombards the surface of electronic components with ions and reactive species. This process effectively removes organic and inorganic contaminants, providing a thorough cleaning without causing damage.
Q: Is Plasma Technology safe for electronic components?
Ans: Yes, Plasma Technology is generally considered safe for electronic components. The process is selective, targeting contaminants without affecting the integrity of the components. Proper parameters must be set to avoid any potential damage, and it is crucial to adhere to manufacturer guidelines.
Q: What types of contaminants can be removed using Plasma Technology?
Ans: Plasma cleaning can effectively remove a wide range of contaminants, including organic residues, dust, oils, and oxides. It is particularly useful for removing stubborn or delicate contaminants that may be challenging to eliminate using traditional cleaning methods.
Q: Can Plasma Technology be used for all types of electronic components?
Ans: Plasma cleaning is versatile and can be used for various electronic components, including semiconductors, printed circuit boards (PCBs), sensors, and more. However, it’s essential to consider the specific requirements and materials of each component to optimize the cleaning process.
Q: Are there any special considerations for implementing Plasma Technology in electronic component cleaning processes?
Ans: Implementing Plasma Technology requires attention to parameters such as gas composition, pressure, and exposure time. Additionally, compatibility with different materials and components should be verified. It is advisable to follow manufacturer recommendations and industry best practices for optimal results and reliability in electronic component cleaning.